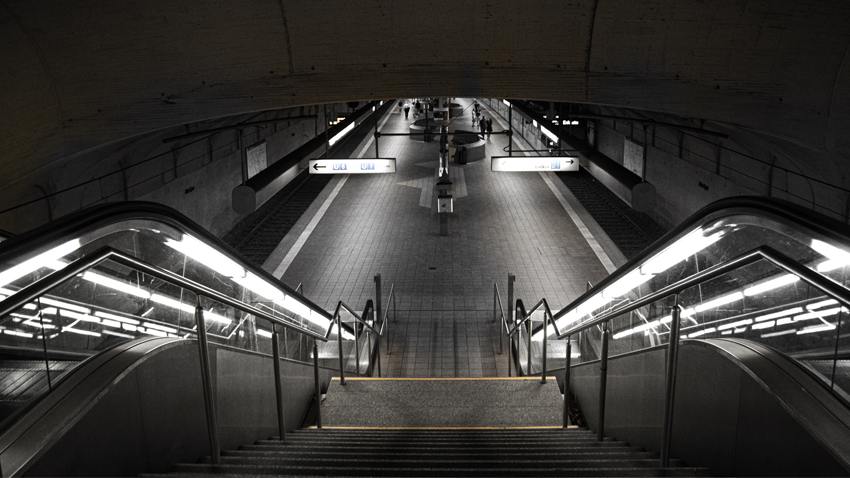
Transportation Session
Language: English
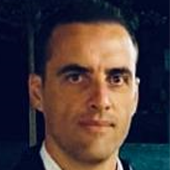
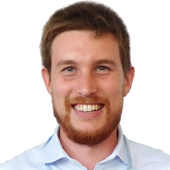
Wartsila Italia S.p.A | Luciano Perinel
EnginSoft | Gianluca Parma
Large bore engine lubrication system: oil flow and pressure analysis by Moving Particle Simulation
Lubrication is a crucial aspect when talking about efficiency and durability of any moving machine parts and, in particular, for large internal combustion engines. Wärtsilä and EnginSoft built a Moving Particle Simulation model (MPS) to analyse the big-end-bearings oil feeding system of an 18-cylinders engine configuration. MPS is a mesh-less method to solve the Navier-Stokes equations which discretize fluid as a gathering of particles. Modelling and simulation of the engine using Finite Volume CFD techniques would be unfeasible due to the motion of the engine parts, which would make the management of the mesh motion not practicable. By simulating the flow through the channels, the Moving Particle Simulation model allowed calculating the transient pressure behaviour in crucial areas of the bearing. Comparison of two bearing designs highlighted differences in terms of pressure stability, peaks and low values that could potentially lead to cavitation issues
Curriculum L. Perinel | Curriculum G. Parma
He was hired in Wärtsilä January the 7th, 2008 as Turbocharging Systems expert, in the Design & Development area of R&D. From January 2008 to November 2014 he dealt with mechanical issues related to Turbocharging System of both small and large bore engines. From November 2014 he is dealing with crankshaft, bearings and gear wheels of small and large bore engines as senior expert in Running Gear Team.
After the Master Degree in Aeronautical Engineering, Gianluca Parma spent two years as research assistant at Politecnico di Milano studying numerical methods for ice-accretion prediction on flying vehicles. From 2018 he joined EnginSoft where he focused on simulations based on the meshless Moving Particle Simulation method, specializing in engine lubrication and cooling applications. Currently, he is Project Engineer at EnginSoft and Technical Manager for the Moving Particle Simulation software Particleworks in Europe.
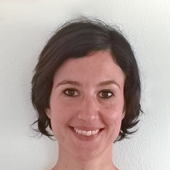
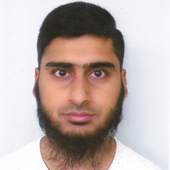
Alfa Laval | Nicoletta Spazzadeschi
Alfa Laval | Danish Taufiq
Validation of a Methanol fuel supply system model of a 2-stroke dual-fuel marine diesel engine
Methanol is recognized as one of the strategic fuels to achieve the ambitious decarbonization goals set by the International Maritime Organization for the next decades. As a leader company in the marine sector, Alfa Laval has experience in designing and supplying methanol fuel-supply systems for marine diesel engines. In the present study, Alfa Laval together with Enginsoft shows the results of the simulation of a methanol fuel supply system currently running on a methanol carrier. Scope of the study is to develop a validated CFD 1-D model, able to reproduce the existing set of data collected from a real plant, both in steady-state and transient conditions, as well as its interaction with upstream and downstream parts of the overall fuel line, from tank to engine. The validated model will allow Alfa Laval to simulate the behavior of the plant under different conditions and to give remote support to customers, setting up the basis for a new digital approach to product development.
Curriculum N. Spazzadeschi | Curriculum D. Taufiq
Nicoletta Spazzadeschi is Senior Process Engineer at Alfa Laval. Graduated in Chemical Engineering at Politecnico di Milano in 2006, she has worked from 2007 to 2017 in process department of an oil & gas company. Since 2017 she is part of the Product Development Team of Alfa Laval, based in Monza (Italy), dedicated to the process design of fuel supply systems for marine diesel engines. Her interests are related to process simulation and to the development of technologies for alternative fuels.
Danish Taufiq - Graduated in Advanced Chemical Engineering from the University of Manchester in 2020, I am currently working as Junior Process Engineer at ALFA LAVAL Fuel Conditioning Systems & Modules Product Development team. I am currently involved in the development of fuel conditioning systems for alternative fuels, such as methanol, LPG and ammonia, with the support of process and computational fluid dynamics simulation environments.
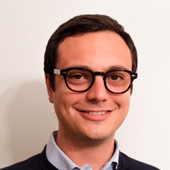
Cubit | Michele Farnesi
An Innovative Optimization Procedure for Supercavitating Wing Sections
The challenging design of a high-performance speed craft, which aims to set the new sailing speed record, requires an hydrodynamics optimization procedure with an innovative approach to obtain the desired performances facing with computational costs and component feasibility. A 2D section is optimized in supercavitating regimes in compliance to structural and manufacturer technological requirements of the section-based wing. The section’s hydrodynamics features are evaluated with a CFD tool; then, thanks to the knowledge built during this project, it is possible to fulfill the lack of know how about supercavitating wings behavior to obtain the section-based 3D wing’s overall performances prediction. The feasibility of the wing is evaluated with a FEM analysis using a custom force imposing method based on CFD outputs. This procedure led to a well-defined and fast design space exploration obtaining a wing Drag reduction of more than 25% respect a reference solution with an imposed target lift.
Michele Farnesi is CFD Pre-Sales Engineer at Cubit. Graduated in Aerospace Engineering in 2019 with final dissertation titled “Numerical Evaluation using DES Approach in Automotive Industry”, since 2020 works in Cubit Fluid Dynamics Division as CFD Engineer, involved especially in CFD and Hydrodynamics consultancy for Syroco focusing on cavitation and supercavitation phenomena in high-performance vessels design. Alongside the technical duties, is in charge of the business expansion of the division.
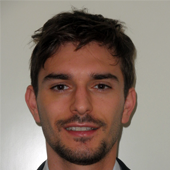
University of Modena and Reggio Emilia | Andrea Fornaciari
Upshifting Next Generation Suspension Design
This study presents the work undertaken by Dana Incorporated to develop a new independent suspension axle for an off-highway vehicle (OHV). This multi-disciplinary simulation activity combines improvements to the kinematic and dynamic performance of the suspension while also examining the constraints of the mechanical design and the hydraulic system, as well as the cost of the suspension. The primary goal of this study was to assess the capabilities of an automated optimization process developed using design optimization software “modeFRONTIER” which integrated several tools including Creo®, MSC Adams®, and Simcenter Amesim®. This project also served to assist Dana in successfully integrating this methodology into future workflow process enhancing independent suspension axles.
Andrea Fornaciari is a PhD student form University of Modena and Reggio Emilia.
His main research field concerns fluid power components and systems for both industrial and mobile applications.
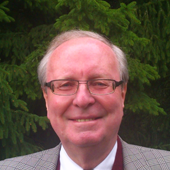
FCMS | Werner Pohl
Environmentally friendly travel bus design of the future
This paper focusses on innovative methods to reduce the CO2-emission of travel busses by new ways to realize weight reduction. A combination of shape variants for load carrying bus sub-structures with a mix of usual mild steel and high-strength stainless steel, making use of a geometry-driven design, fast running surrogate models, comprehensive design optimization, and an automated refeed of optimized surrogate models into detailed correct geometry models for validation analyses unveals weight potentials, which cannot be discovered by traditional CAE methodology. Technically, the key is a full associativity between CAD and CAE. Commercially, the cost aspects are made part of the design process. Both material and welding cost have been considered. Loadings are stress, fatigue and rollover based on internationally accepted layout criteria for travel busses.
Dr.Pohl, PHD in physics, native Austrian, with over 30 years of industry experience and 7 employers in telecommunications and mechanical industry (CAD-CAM-CAE-CAT).
Experienced with functions like CEO, GM / MD for Sales and Development Divisions, Corporate VP and Regional VP (e.g. Europe, Asia); job locations in Germany, The Netherlands, Belgium and Japan.
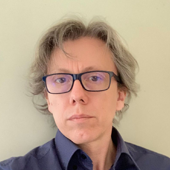
RICARDO | Pietro Del Negro
Fatigue Analysis on a Motorcycle Frame
Fatigue Analysis on a Motorcycle Frame using FEMFAT. The Fatigue analysis was performed on the structure itself and on the welded seams. In the presentation will be shown the comparison between numerical results and phisical fatigue tests results performed on the motorcycle.
I’m Pietro Del Negro, I’m a Mechanical Engineer and I work in RICARDO Motorcycle in the CAE Department. I’m responsible for structural analysis of frames and other structural components of a motorcycle. Static, Dynamic and Fatigue Analysis performed on these structures are fundamentally to obtain the best final product in terms of safety, reliability and quality reducing the development and production costs.
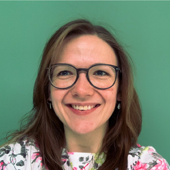
Monolith AI | Isabel Ashworth
Predicting 3D fields of transient CFD simulation data using deep learning to accelerate the development of Internal Combustion Engines
As in many engineering industries, development timelines for Internal Combustion Engines (ICE) are too strict to allow for full exploration of design permutations through large volumes of simulations and physical tests. To address this challenge, this study demonstrates how the performance of new ICE designs simulated under new conditions can be predicted using machine learning. Using a historic dataset of transient CFD data, deep learning models prove to be able to accurately predict the transient evolution of scalar performance metrics, but also entire 3D flow fields of simulation data. With such a simulation-machine learning approach, a complete understanding of the correlation between design variables and simulation outcomes is established. This allows finding performance-optimised designs for target simulation metrics in near-real-time. This study was developed by Monolith AI in partnership with Siemens Digital Industries Software.
Isabel Ashworth is Senior Project Engineer at Monolith - an AI platform that empowers engineers to build products faster. Isabel completed a Masters in Physics at the University of Manchester, where she investigated “Transport Signals In Poor Visibility”, specifically looking at the propagation of different light sources through fog. Isabel specialised in theoretical fluid dynamics and climate CFD throughout her career in the automotive industry, and was awarded the TechWomen100 Award in 2019. As Senior Project Engineer of Monolith, she leads different projects with clients and ensures that the AI technology developed in the company is relevant and valuable for engineering companies.