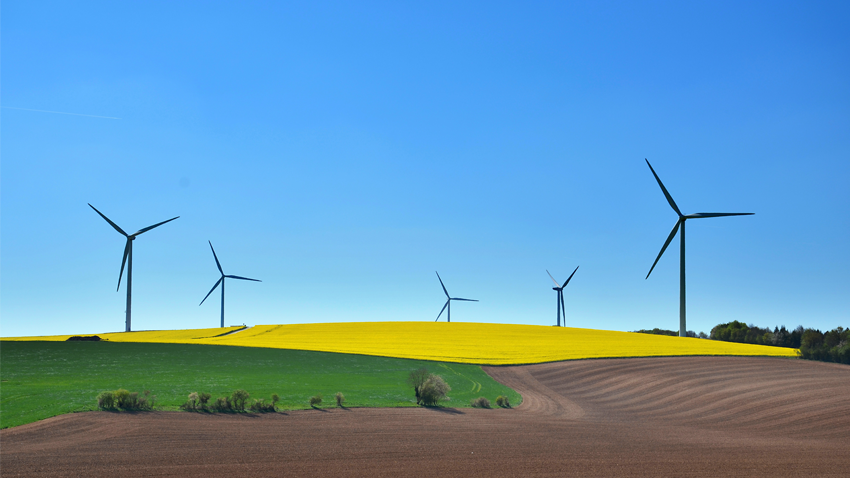
Energy Session
Language: English
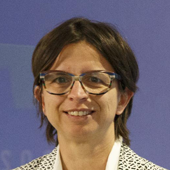
Keynote Speaker
ERG Group | Emanuela Delucchi
Engaging in green transformation: lessons and insights from ERG
The ERG Group is an independent power producer from renewable sources: wind, solar, hydro and thermoelectric co-generation with high efficiency and low environmental impact. The challenges of sustainability and energy transition are key issues for ERG, which proposes to act as a Green Leader to guide companies that are undertaking this critical challenge in their transformation journey by sharing insights, experiences, and advice and opportunities.
Born in Genoa on 18th December 1975, she graduated in Economics from the University of Genoa in March 1999.
She joined the ERG Group in February 2008 where she is currently Chief ESG, IR & Communication Officer, with the mission to develop and monitor the implementation of the ESG (Environment, Social and Governance) Plan and to ensure the development of integrated communication strategies and solutions to guarantee the extensive promotion of the Group with the financial community and all stakeholders, maximising the value of its reputation and protect ERG’s company image.
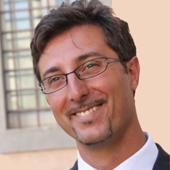
RINA Consulting | Emiliano Costa
Assessment of harmful fumes dispersion in the nearby of building HVAC system elements using CFD
The numerical study described in this paper aimed at predicting the dispersion of toxic fumes exiting three fume extract discharge duct terminations located at the roof level of the building called “One Springfield Drive” located in Leatherhead (UK). The principal objective of the simulations was to evaluate if the height of chimneys is appropriate to prevent that harmful fumes entrain at the two clean air handling intakes of the HVAC system. Four conditions of the wind were selected and analysed through a commercial CFD software, because judged to potentially represent a danger condition for safety considering the relative position of air intakes and chimneys as well as natural and artificial elevations around the buildings of interest. To evaluate both qualitatively and quantitively if a dangerous condition could occur, fumes concentration at air intakes was computed and other relevant results, such as the streamlines from the chimneys outlet and volume occupied by fumes, were provided.
Emiliano Costa is a Principal Engineer in the Industrial Design & CAE team at RINA. He has a Ph.D. in Energy and Environmental Engineering and over 15-years of industrial experience in the CAE sector. He specializes in computational fluid dynamics and computational structural modelling and analysis. He used to be the coordinator of the RBF4AERO project and the Principal Investigator of the Experiment n. 906 of the FORTISSIMO project.
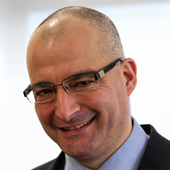
RBF Morph | Marco Evangelos Biancolini
Simulation and mitigation of Vortex Induced Vibrations by means of high fidelity FSI simulation and advanced mesh morphing
In this study we face a complex and challenging problem: the control of Vortex Induced Vibrations (VIV). The fluid structure interactions involved poses two kind of problems. First of all skills of structural and fluid
analysts are needed and a proper interaction of experts is a paramount to be successful. Furthermore, an accurate modelling requires state of the art tools for the computational fluid dynamics and for the computational structural mechanics to be combined together.
Advanced mesh morphing enabled by radial basis function is a key enabler in this field: it allows to create an efficient and fast workflow for a strong coupled FSI analysis and, at the same time, to make such workflow parametric with respect to the design so to have, at the end, the ability to steer the design toward the desired VIV behaviour. We adopt structural modes embedding to make the fluid solution "flexible". The dynamic features of the system are computed with the FEA solver Ansys Mechanical, embedded in the fluid solver Ansys Fluent by means of the mesh morphing software RBF Morph. The shape parametrisation technology offered by RBF Morph is then used to steer the design. The method is demonstrated for a specific application: the design of a thermowell.
Dr. Marco Evangelos Biancolini is an associate professor of Machine Design at the University of Rome “Tor Vergata”. The main research interest is on engineering applications of fast radial basis functions, mesh morphing and its application in the field of shape optimization and of reduced order model for the definition of digital twins.
Owner and developer of the industrial software RBF Morph, partner of Ansys and honorary member of the Technet Alliance.
Principal investigator of the 4 years ITN-EID H2020 project “Medical Digital Twins for aneurysm prevention and treatment” MeDiTATe since 2020.
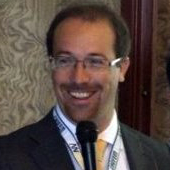
SAECON Sagl | Davide Valtorta
CFD Analyses of ventilation systems in livestock carriers
The performance of the ventilation system in livestock carriers represents a key factor for animal welfare during long overseas transports. Voyages can last up to 2-3 weeks for typical trading routes crossing the equator, where heat stress events can potentially occur, representing a serious threat for the animals on board.
CFD simulations can be used for the design and optimization of these ventilation systems, improving performance, reducing operating costs, and most importantly increasing animal welfare. CFD analyses were carried out on large livestock carriers to obtain homogenous airflow distribution across all pens, to improve energy efficiency by reducing pressure losses in air ducts and to assess re-ingestion of exhaust air, maximizing fresh air circulation. Examples of CFD analyses carried out on ventilation systems of livestock carriers trading from Australia will be presented, along with experimental results obtained on board, demonstrating the importance of CAE simulation.
Engaged in the business development of since 2015, with more than 15 years successful experience in consulting companies providing CAX engineering services (software, consulting projects, technical trainings, customer service for CAD, CAE, CAM) to high-tech companies in Switzerland, Italy and Germany.
R&D experience at academic and industrial level in international environments, able to work and deal with high-level professionals in complex projects, strong analytical skills. Management and business administration skills enriched with an Executive MBA degree.
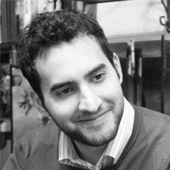
University of Rome Tor Vergata | Corrado Groth
Reshaping the Tokamak TF Coil of DEMO with high fidelity multi physics CAE and advanced mesh morphing
The DEMO Tokamak represents a major challenge under the technical and technological points of view. It is evident that such a race can be won only with an effort up to the challenge at each step of the roadmap, starting with the design stage. This entails the deployment of the most effective design tools available in the CAE environment. This paper shows the optimisation strategy adopted for the TF coils of the ADCs, searching for the best compromise between electromagnetic (EM) and structural compliances. A continuous transformation, based on mesh morphing enabled by the tool RBFMorph, turns the baseline FE model into its bending-free counterpart, with a series of intermediate configurations available for EM and structural investigations as output. A candidate coil is determined for each configuration as the one experiencing an acceptable stress level. Static membrane stress levels during magnetization could be reduced significantly from more than 700 MPa to below 450 MPa.
Corrado Groth is a researcher in Machine Design at the University of Rome “Tor Vergata”, where he took its PhD cum laude with the dissertation “Adjoint-based shape optimization workflows using RBF”. Main thread of his research is the advanced use of Radial Basis Functions (RBF) in mechanical engineering. Some fields of research, between others, are Fluid Structure Interaction (FSI), Fracture Mechanics (FM), fluid dynamic and structural shape optimization using zero order and gradient-based methods. Evolutionary optimization workflows have been developed with adjoint and Biological Growth Method (BGM) approaches.
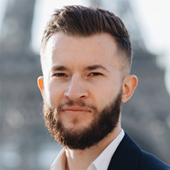
SDC Verifier | Roman Samchuk
Structural Verification of the FEA Models according to the Oil & Gas Industry Standards
To ensure safe and continuous operations, multiple different structures in the Oil and Gas Industry must be analyzed with the help of the FEA method. Finite Element Analysis software is a must during the design process, it helps to simulate the behavior of the structures and indicates the possible problem spots. But to validate and certify the structure engineer also has to prove that it is safe against multiple different failure modes like beam buckling, joint strength, fatigue, stability, plate buckling, weld strength, etc. These checks are usually prescribed in different Industry rules by ABS, DNV GL, Bureau Veritas, and other certification societies. In this presentation, we will go through the main problems and struggles of the structural verification of the FEA results according to the Oil and Gas Industry standards. We will discuss a workflow that helps to simplify the analysis, avoid errors, and minimize the routine.
Roman Samchuk is the Engineering Projects Manager at SDC Verifier.
With 6+ years of experience in Structural and Mechanical Engineering, Roman leads a team of engineers solving the most complicated engineering tasks for customers globally.
In addition to projects management, he is deeply involved in engineering process with focusing on the beam buckling, fatigue, structural stability, and non-linear behavior of the structures.
Being an expert in the FEA calculations and verification according to standards, such as Eurocode, AISC, API, DNV, ABS, and many more, Roman and his team have completed more than 50 projects over the past two years in the Heavy Lifting, Offshore and Marine, Oil and Gas, Civil and Structural Engineering and Machinery Equipment industries.
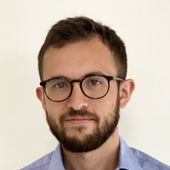
Phi Drive Srl | Liborio Borsellino
FEM modelling of energized lip seals for oil and gas industry
PTFE is a material which is widely implemented in the oil and gas industry for the production of energized seals and gaskets, thanks to its properties like low coefficient of friction and chemical inertness. Seals are used to prevent leakage and mechanical failure at the connection between valve and pipe, in a wide range of working conditions. In particular, seals are exposed by one side to the high pressure and temperature fluid and to the other side to the atmosphere condition. This difference is traduced to high load on the seal that may be subjected to excessive deformation and stress. Moreover, high pressure fluid may enlarge the gasket seat, increasing the risk of leakage, mechanical failure and partial extrusion. On the other side, it must be considered that the necessity to reduce encumbrance and costs by producing thinner and thinner seals without detriment to the safety of the application. A good way to reach this goal minimizing timing and prototyping cost is to use FEM analysis. Phi Drive, in collaboration with Esa srl, has developed a dedicated FEM model which reproduces the working condition of energized seals and allows determining the range of gasket seat width considering the worst working condition in terms of fluid pressure, temperature and construction tolerance. The model is based on Multilinear Isotropic Hardening to define PTFE stress-strain behavior and on variable friction contact to describe the interaction between the gasket and surrounding walls. For every seat width, the model computes different crucial indicators such as maximum stress, length of the extruded part of the seal and shearing force that may cause cutting of the gasket. As long as all indicators are below their limit values, adjusted for a proper safety factor, the energized seal is considered safe. Vice versa, if at least one of the indicators is beyond the limit the seal is not considered safe anymore. Our final article will talk in detail about this project, showing also pictures and graphics of the obtained results.
Liborio Borsellino holds Master Degree in Energy Engineering from the Politecnico di Milano. He currently works as Simulation Engineer in Phi Drive Srl, R&D company part of Gruppo Comestero Sistemi. Liborio provides technical consultancy either for Phi Drives internal products or for third part companies. In particular, by using CFD and FEM analyses, he performs optimization and adjustment on the design of products to solve fluid-thermodynamics and mechanical issues. He participated to the PRE2POS Project funded by EU Horizon 2020, developing an ultrasonic piezo-electric motor for space applications.
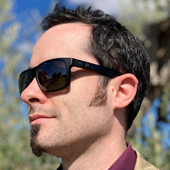
Dassault Systèmes Italia | Lorenzo Maria Pii
Model-based Integration of Flow and Acoustic Performance Optimization for Axial Fans in Building HVAC Systems
Heat ventilation and Air Conditioning (HVAC) systems are used in 87% of homes in the US, and represent on average 12% of household expenditures. This breadth of usage means that even small changes in technology can have a huge impact on the footprint of HVAC systems on our environment. Such an impact has led to the progressive ban of Ozone depleting refrigerants in chiller circuits following the Montreal Protocol and Kigali Amendment agreements. This change is affecting the performance of the chiller circuit, and therefore motivating a re-dimensioning or re-design of the full HVAC system. Aside from the chiller circuit, fans themselves are typically responsible for 34% of the average energy consumption of HVAC systems, and are therefore a good subject of work when targeting improved overall system efficiency. Hence, effective design of efficient fans would require iterating towards a better design, typically leveraging a three-dimensional simulation of a rotating geometry. Furthermore, the performance of these fans is highly dependent on the integration to the full HVAC system. Tackling these types of issues often require representing the HVAC system performance as a set of 1D reduced-order-model nodes. Meeting these types of energy efficiency objectives requires a new approach to system integrated component design. In this paper, we will present aspects of such a design loop, focusing on the aerodynamic and aeroacoustic CAD driven optimisation of an axial fan In a second part of the paper, we will include the impact of the fan design in the overall HVAC system performance, represented as a reduced order 1D model. We will show that such development can be organized effectively using a centralized platform, ensuring all key requirements are met.
Lorenzo graduated in Aerospace Engineering at the University of Pisa and he has always been very fond of Fluid Dynamics. After taking part in the development of a number of motorsport cars, he joined Exa in Paris in 2012 where he was responsible for the heavy vehicle industry especially for the agricultural machines and railway sectors. He moved back to Italy in 2015 to lead a team to take care of the EMED market and customers and became part of SIMULIA since the acquisition of Exa from Dassault Systèmes in 2019.