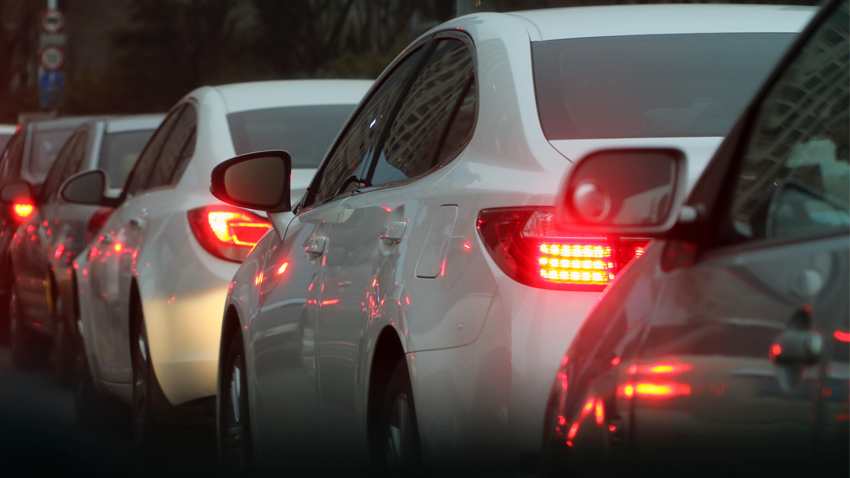
Automotive Session
Language: English
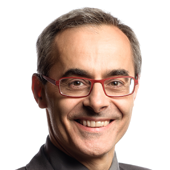
Keynote Speaker
Modelon | Hubertus Tummescheit
Decarbonization through System Simulation
The urgent trend to decarbonize our consumption of energy will require rapid and sustained innovation across all industries. It also leads to tighter integration and more system-level dependencies across formerly separate industries: electric cars serving as batteries for the power grid, green hydrogen, produced from renewable energy to power aircraft, and green ammonia as fuel for the shipping industry are examples of tighter integration between industries, and also the growing importance of system thinking. System simulation is necessary to support the digitalization of the design and innovation processes that will help us to achieve the necessary efficiency and speed of innovation. In addition, the tight integration between processes makes it more important to add operational optimization of these systems to the tasks that the engineering community will have to solve. This new world of high integration and quick innovation requires more from the next generation of CAE tools: seamless collaboration between people and easy integration between tools become ever more important. Open standards and emerging cloud-native web-based tools supply the technology foundation to collaborate between teams, and between OEMs and suppliers. Engineering Digital Twins are where traditional CAE-simulation combines with web technologies to create new business models, through operational optimization, predictive maintenance, or other insights into the actual usage of technical systems. Digital twins give us engineers a new way to close the loop between the actual usage of our products, and the next generation of them. Let’s use them! We will show how system simulation and optimization can be used to support innovation for decarbonization and present concrete examples from the automotive, aerospace, and energy industries. The examples will also show how simulation for engineering design leads to more value when it is reused in engineering digital twins.
Hubertus Tummescheit is the Chief Solutions Officer of Modelon, President of Modelon Inc., and a co- founder of Modelon. Modelon provides software solutions and expert services to organizations that use model-based simulation tools to design and develop technical systems.
He has been involved in the Design of the Modelica language from the beginning and is the developer of a number of open source and commercial Modelica Libraries in the energy and HVAC domains. In 2003 he worked as a research scientist at United Technologies Research Center and returned to Sweden in 2004 to start Modelon AB, the first company fully dedicated to tools and services based on Modelica and FMI. Dr. Tummescheit is also a member of the board of the Modelica Association, and of the FMI steering committee. He is active in the future development of both standards.
Dr. Tummescheit has served as the CEO of Modelon AB from 2004 to 2012 and moved to Hartford, Connecticut in 2013 to establish Modelon as a leading force of innovation in system simulation in the United States of America.
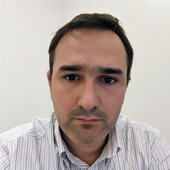
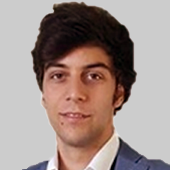
Nidec PSA Emotors | Ioan Deac
EnginSoft | Michele Merelli
E-drives spray cooling optimization by Moving Particle Simulation
Over the next decade, e-drive units for hybrid and electric traction will continue to evolve towards the industry-specific requirements: increase in power density, efficiency and reliability, while reducing the costs. On the other hand, the Electric Vehicles (EVs) and hybrid platforms are expected to become mainstream even for less expensive cars with high production volumes placing even more pressure on the cost of materials and process for the e-drives. Thermal management of the e-drive is a crucial factor affecting both the performance and life. Internal spray cooling concepts are already used by several players in the automotive and transportation sector in order to cool down the e-drives components with impressive results. Even more, the growing integration of the e-drive and transmission units allows for the use of the transmission fluid as the coolant in the e-motor. The development of this type of cooling is still very dynamic with multiple players exploring the limits of this technology (see recent patents). Nidec PSA EMOTORS (EMOTORS) joint venture took on the challenge of developing and producing high-performance and competitive e-motors, bridging e-motor design and manufacture know-how and automotive expertise together in a very ambitious enterprise. The company has adopted simulation techniques since the early stages of the development process to drive the thermal design of their line of e-motors and to predict and optimize the motor temperature. This presentation will focus on the simulation of oil distribution system in the motor, and its use on predicting the heat removal and temperature distribution in the motor. Fast comparison of different concepts and the choice of the best design solution is done by running mesh-less CFD simulations using the Moving Particle Simulation (MPS) method, which is ideal for simulating oil splashing and jet impingement phenomena in the e-drive. In this paper engineers from EMOTORS and EnginSoft will explain the simulation process that allows the inspection of the e-drive virtual prototypes and the improvement of the final design.
Curriculum I. Deac | Curriculum M. Merelli
Ioan Deac joined Nidec in 2012, as a thermal and CFD engineer for electric motors and generators. In 2018, he was part of the engineering team that joined the new joint venture with PSA to produce electric drivetrains. Currently, he is responsible for a team of thermal of CFD and thermal engineers at Nidec PSA Emotors in Carrieres-sous-Poissy (Paris area), France. He achieved his Master Degree in “Renewable Energies” at Technical University of Cluj-Napoca (Romania) after the Bachelor in “Thermal Systems”. He is interested in CFD, thermal modeling, optimization methods and electric powertrains with a strong emphasis on practical applications and validation.
Michele Merelli joined EnginSoft in 2019, after an internship in ABB. He achieved his Master Degree in The Netherlands (Rijksuniversiteit, Groningen), after a Bachelor in Materials and Nanotechnology Engineering in Italy (Politecnico di Milano, Milan). He focused on simulations with Moving Particle Simulation ever since joining EnginSoft, specializing in e-motor cooling and thermal management simulations, supporting several companies with remote assistance and onsite visits across Europe. Currently, he is Project Engineer in EnginSoft and Pre- and Post- Sale Manager for the Moving Particle Simulation software Particleworks in Europe.
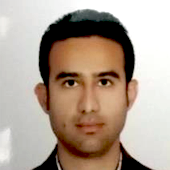
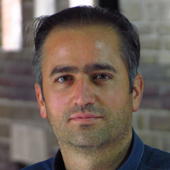
University of Modena and Reggio Emilia | Moslem Molaie
University of Modena and Reggio Emilia | Farhad S. Samani
Loaded tooth contact analysis and dynamic investigation of Spiral Bevel
To transfer the power between non-parallel shafts, bevel gear pairs, especially spiral bevel gear pairs (SBGs), play a significant role in transmission systems. SBGs are smooth, quiet, and can bear high levels of torque and power thanks to a high contact ratio, although their complex geometry requires recognizing the parameters which affect the transmission efficiency and durability. Vibration is one of the main issues since it affects the stress distribution, contact pressure, and the fatigue life of a geartrain. Several parameters, such as the time-varying mesh stiffness and the gear mesh transmission error, exert a prominent influence on vibrations and are sources of driveline noise. Therefore, Mesh Stiffness (MS) and Transmission Error (TE) are two key parameters that take an intense research activity. A wide range of methods has been employed to calculate these two parameters. To calculate the static transmission error (STE) and the MS of a gear pair, the loaded tooth contact analysis (LTCA) has to be carried out. The LTCA could be done through different methods, e.g. finite element method (FEM), experimental method, analytically. In the last decade, different software have been released and developed. These software employ FEM, standards (for instance, ISO), or both methods to extract MS/TE for different gear sets. In this study, both STE and MS are calculated using different methods, and the results comparison is presented from both points of view, statics and dynamics.
Curriculum M. Molaie | Curriculum F. S. Samani
Moslem Molaie Emamzadeh graduated in Mechanical Engineering-Applied Mechanics as Master of Science from Shahid Bahonar University of Kerman, Kerman, Iran.
He is currently involved in a project focused on "Cost-effective multi-sensor diagnostic-prognostic integrated system in mechanical drives for Industry 4.0" at the University of Modena and Reggio Emilia, Italy.
Farhad S. Samani
Associate professor at Mechanical Engineering Department
Shahid Bahonar University of Kerman (Iran)
Visiting Professor, at Department of Engineering "Enzo Ferrari“ University of Modena and Reggio Emilia, Italy
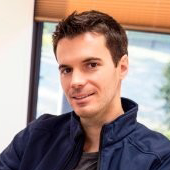
TotalEnergies | Jonathan Raisin
Electric motor cooling simulation : direct vs indirect
In a global energy transition program, electric and hybrid vehicles will sharply increase in order for the OEMs to meet CO2 regulation targets.
Today, electric cars are still mainly manufactured with an indirect cooling system for the electric engine, using water or air. But performances improvement will lead to the evolution of the cooling system towards a direct cooling system, which is more efficient.
It is in this context that TotalEnergies tried to better understand through simulation approach the efficiency of a direct oil cooling system, and show that it is, and will be the future for electric and hybrid cars.
PhD 2007 – 2011: Grenoble electric engineering laboratory (G2Elab)
Design and operation of numerical models and experimental prototypes to establish a criterion for estimating the crude oil dehydration potential of the latest generation of electro-coalescers. Work carried out within the framework of an international project (Sintef, BP, Shell, Saudia Aramco, Petrobras, Statoil, AkerSolutions...)
2011 – 2013: Contact and structural mechanics laboratory at Insa Lyon/CNRS
Development of a numerical tool for the simulation (TEHD) of lubricated mechanical systems. Application to the study of the thermal and mechanical stresses undergone by lubricants in automobile racing engines
2013 – Today : Numerical Simulation Manager at TotalEnergies
Modelling and simulation of lubricated mechanical systems.
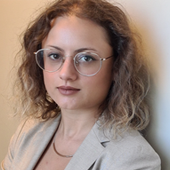
Capgemini Engineering | Caterina Magro
Full CFD Multiphysics Analysis of a Body in White Paint Dipping Process
A 3D-CFD study is performed using Star CCM+ to simulate a tank dip-in-out event of a vehicle model (body-in-white, closures-in-white, skid), in order to establish the effectiveness of liquid jets in dislodging the entrapped air from the traps/pockets with focus on the underbody castings. The analysis is set for viscous, turbulent, transient, 2-phase (e-coat liquid and air) flow, with no-slip boundary conditions at the surface of the vehicle and tank. The total simulated time covers the vehicle motion from the initial position until full emersion (320 seconds), and the drainage phase (60 seconds). The results show how the arrangement of the jets can affect the creation of air traps in specific areas of the body with noticeable improvements. The overall reduction of the air traps on the BIW is more than 50%; the remaining traps are due to the position and the direction of the jets that are not effective. The results of drainage phase show the areas of greatest accumulation of paint.
Caterina Magro is a CFD Consultant at Capgemini Engineering in Turin since 2018. As part of a CFD/CAA team, she works in different fields of the Mechanical Industry. She has experience with aerodynamic, thermal, multiphase and multi-components fluids simulations. She got also familiar with acoustic analysis.
Graduated in 2017 at Politecnico di Torino in Aerospace Engineering, during her Master Degree she experienced wind tunnel methodology and data acquisition and correlation.
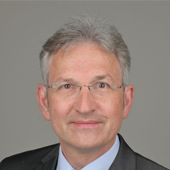
ISKO Engineer | Michael Probst
CAD-based automated shape optimisation for non-experts
Simulation has become a necessary part of the process at almost every stage of product development. However, it is experts in simulation that often become the bottleneck in design evaluation and thus development progress. The optimisation of design variants is one of the great advantages of this technology, yet only a few experts use it regularly. One stumbling block to widespread use of optimisation is the required re-design of the optimised geometry approach, which must be interpreted and rebuilt in a CAD tool. A promising approach to solving problems such as lack of experts, work overload due to routine tasks or non-applied state-of-the-art technologies (such as optimisation) lies in the standardisation and automation of expert processes and their provision as "expertise as a service". A special combination of geometry-based parameterisation, simulation-ready pre-processing and automated, interactive optimisation processes provides a leading-edge possibility for every engineer to perform even complex simulations and optimisations. The presentation shows the approach and an example of what an applicable implementation looks like.
Since 1.8.2020: Head of Business Development and Sales at FCMS GmbH
• Engineering Services, CAE Process Optimisation
• New CAE technologies, data driven applications for CAE
• Simulation Management, CAD speed-up
1.1.2000 - 31.7.2020: Executive Board of ISKO engineers AG
• Management Finances, Personnel,
• Keyaccount Audi, VW,
• Sales and Business Development
1.10.1996 - 31.12.2000: Self-employed simulation engineer as partner in ISKO GbR
1.4.1991 - 30.9.1996: Employed simulation engineer (project acquisition, calculation, implementation and conclusion, technical management)
10/1983 - 1/1990: Studies of mechanical engineering at the Technical University of Munich with diploma degree
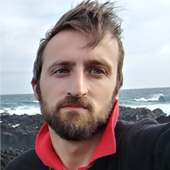
STELLANTIS | Emiliano Di Tullio
HVAC technology to enhance MHEV performances
HVAC system has been helping people since the early years of the 20th to get better comfort in cars, in houses, outstanding cold temperatures in fridges, but nowadays it is called to allow "better comfort" energy storages, too.
Let's see how the HVAC technology and components can be used, as they are, rethinked, or combined together in MHEV applications.
Emiliano Di Tullio is a Mechanical Engineer, born in 1980, in Civitanova Marche(MC).
He studied at Università Politecnica delle Marche.
He started to work in Ferrari as consultant of Delphi as an Application Engineer, working on several project like F430, F599XX and A1Gp project.
He moved on 2011 in Aprilia as consultant of Altran to design and manage wiring harness of Aprilia and Guzzi bike.
In 2011 he joined Fiat, now Stellantis, covering different positions.Today He is a Senior Virtual Analyst.
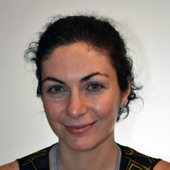
Optimad Engineering | Angela Scardigli
A Numerical-Experimental Methodology for vehicle noise prediction at constant speed
Vehicle interior noise plays an important role in the passengers perception of vehicle quality and acoustic comfort awareness is growing among customers: as a result, the analysis of acoustic sources and the development of sound packages have become strategic in the automotive design process. For ICE cars, the engine and exhaust system are the main sources of the vehicle overall noise, but these components are no longer present in electric cars, where the noise comfort level is determined by the aerodynamic and rolling noise. In this frame, we developed a numerical approach based on transient CFD and SEA coupled simulation and completed with experimental measurements, permitting to model the aeroacoustic component, but also to consider road noise. Numerical prediction was validated against interior noise measurements at constant speed for a SUV, showing how this methodology can be successfully used to design proper sound packages for noise reduction in the audible frequency range.
Angela Scardigli graduated in Aerospace Engineering from Università di Pisa in 2012, and later obtained a PhD in Pure and Applied Mathematics within an industrial apprenticeship programme jointly supervised by Politecnico di Torino and Optimad.
Since 2013 she has been part of Optimad R&D team, where she is responsible for research at the proof of concept stage. Her area of expertise includes optimization and fluid dynamic simulation, with focus on automotive, naval and aeronautical applications.
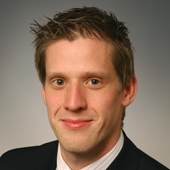
Dassault Systèmes | Enno Lange
Non-Parametric Rotor Shape Optimization of an EV-Drive Permanent Magnet Synchronous Machine
The design of an electrical machine is a trade-off between multiple requirements rooting from different physical disciplines subject to strict cost and manufacturing considerations. Throughout the past decades, engineers and scientists aggregated a vast amount of knowledge in design methodologies and processes to accommodate the various competing requirements. Usually, the design process starts with the conceptual phase addressing the overall topology of a drive train and possibly moves on to a trade-off analysis of various machine types. The next design step is typically the synthesis of the initial design for a specific machine type defining the starting point for numerical optimizations of various physical disciplines e.g. electromagnetics, thermal, structural, etc. To this end, parameterized models in CAE environments represent designs of electrical machines allowing for highly automated design space explorations at the cost of computational power. The design space exploration will allow for a trade-off study and help choosing an optimized design candidate. However, the choice of the fundamental parametric building blocks and the associated few number of design parameters limits the design space and the overall quality of the design. Thus, the experience and knowledge of the engineer creating the CAE model and corresponding optimization parametrization is a limiting factor for the optimization process. The present work suggests a non-parametric shape optimization of the rotor surface for a permanent magnet synchronous machine for eliminating the limitation of parametrized optimization for CAE models of electrical machines. A parametrically pre-optimized rotor is applied as initial design for a non-parametric surface shape optimization that minimizes the torque ripple and maximizes the average torque as an objective function. Additionally, a strength constraint enforces the mechanical stress not to exceed a given tolerance. The present optimization approach builds on numerical FE analysis for the electromagnetic and structural domain, respectively. The optimized rotor shape is determined using mathematical programming and adjoint sensitivities for electromagnetic design responses for objective function and structural strength constraint. An example will illustrate the proposed approach. The paper concludes with an outlook addressing other important key performance indicators e.g. iron losses or nodal forces. Noise and vibration, and system simulation integration highlight further areas of application.
This full presentation is not available
Enno Lange received his diploma in 2006 and in 2012 his doctorate in electrical engineering from the RWTH Aachen University, Germany. During his studies, he focused on the numerical field computation for electrical machines and published various peer-reviewed papers on that topic.
In 2012, he joined the Computer Simulation Technology (CST) AG in Darmstadt as a software developer and has since then held various positions in research and development. With the acquisition of the CST AG by Dassault Systèmes he continued working as a Senior Application Manager within the SIMULIA brand of Dassault Systèmes developing integrated end-to-end simulation workflows for electrified drive trains for the transportation and mobility industry.